Top Considerations for Smooth Waterjet Machinery Operations
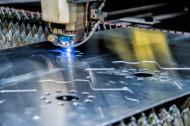
Abrasive waterjet operations call for a thorough grasp of system installation requirements and environmental implications. System installation flaws may bring about extra cleanup costs after abrasive cutting. The costs be addressed by taking into consideration cleanup requirements for the abrasive cutting machine ahead of time and incorporating the cleaning process into the machinery setup.
Environmental Factors
If cutting using a waterjet cutting systems, as much as 2 GPM of overflow water can be produced form the cutting tank. As per local regulations, it may be necessary that the water undergoes processing before it's let into the drainage system. Before buying the machinery, ensure to review local water regulations, especially keeping in mind the type of material that's going to be cut. A waterjet cutting process may generate a fine coarse dust that will cover the surrounding area.
Abrasive Disposal
Waterjet cutting also produces a substantial amount of waste particles, which are removed from the system by emptying the cutting tank periodically. The installer must take into account EPA and local waste disposal rules, particularly if the material being cut is featured on an environmental watch list. The accumulated debris may be removed via manual shoveling of the tank or by means of several automatic debris removal systems. While the manual option involves no extra costs, it's lengthy and tedious.
Abrasive Suction Systems
Waterjet cutting equipment needs an abrasive suction system, which comes in a variety of types, such as small venturi versions that are positioned manually in a tank and larger fixed array types that have mixing eductors for stirring up particles settled at the bottom of the tank. High capability diaphragm pumps may be employed to pump the stirred up mud via a cyclone separator, through which mud is separated from the slurry material and water is supplied back into the cutting tank.
Dredge Conveyors
The omax waterjet cutting process also generates garnet particles, which can be removed using dredge conveyor systems. The conveyor system is incorporated into the cutting tank. The conveyor extends from the end of the tank set up and empties into a separate container. The tank structure is built with a slanting floor to permit transmission of garnet debris to the dredge conveyor at the center of the tank. The conveyor system should come with a protective cover and be built to stand abrasive conditions at the bottom of the tank.
Adherence to requirements for installation of waterjet cutting systems will ensure low maintenance costs and compliance with environment regulatory authorities.